Equipment
High quality Multi-ply rubber conveyor belt production process and required production equipment
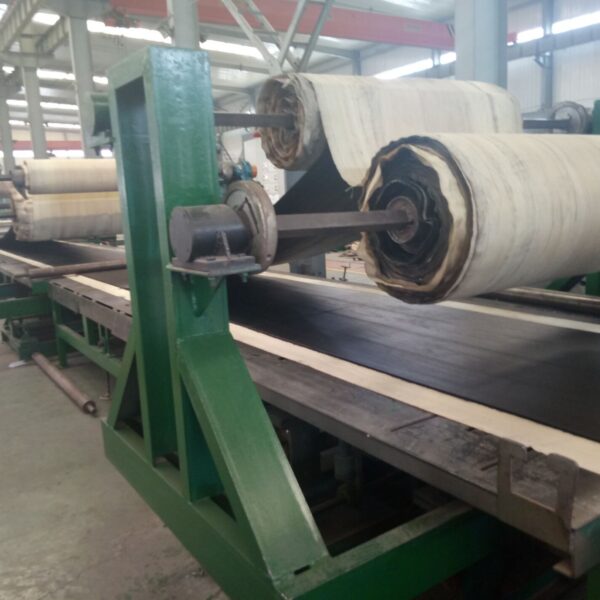
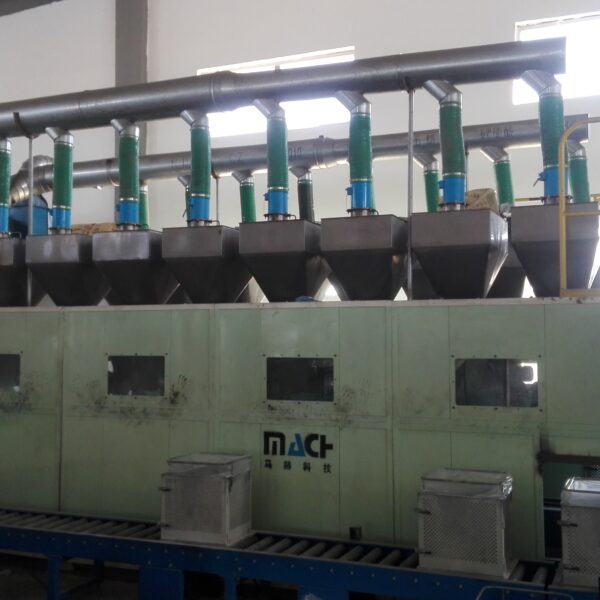
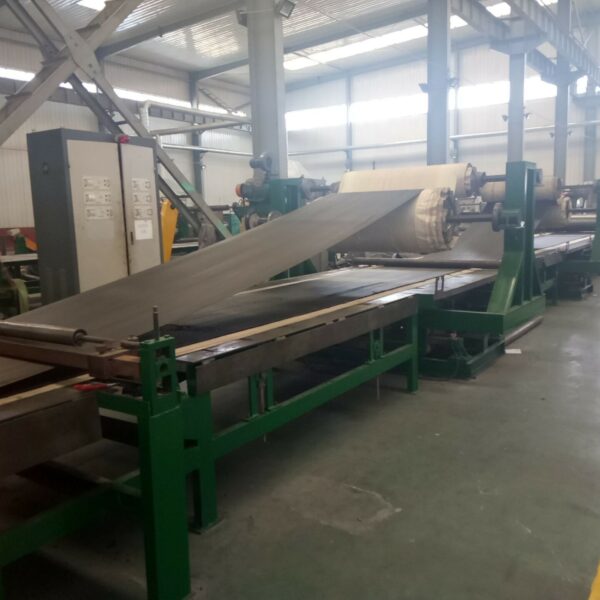
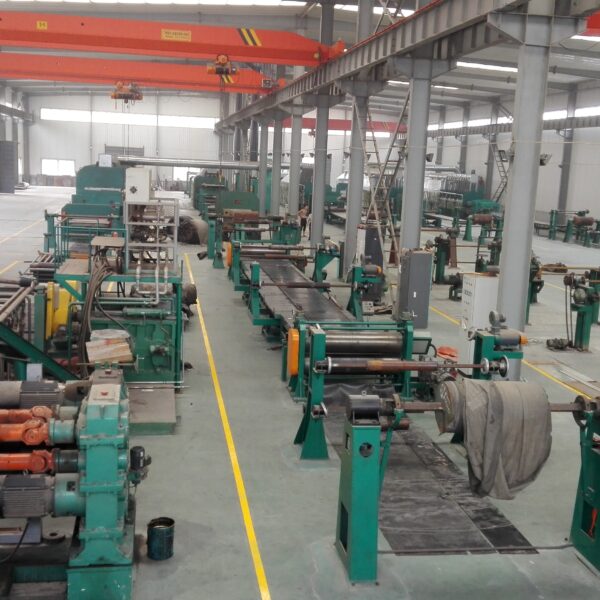
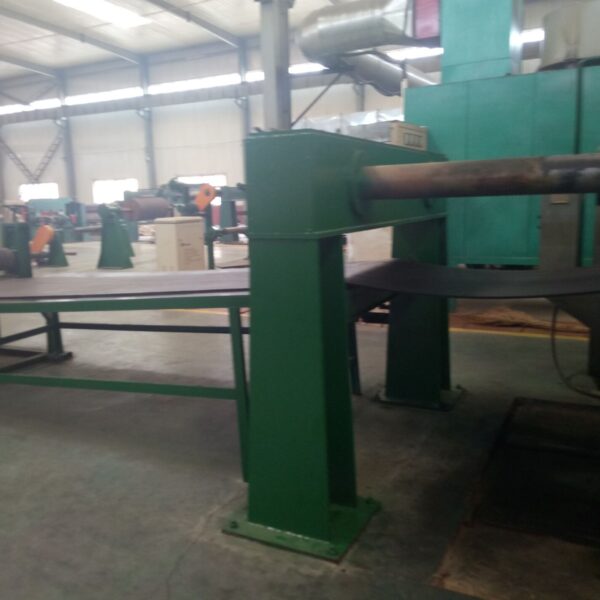
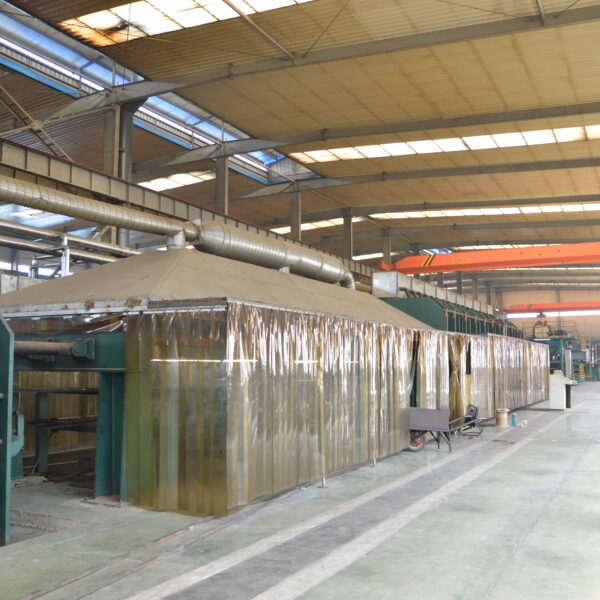
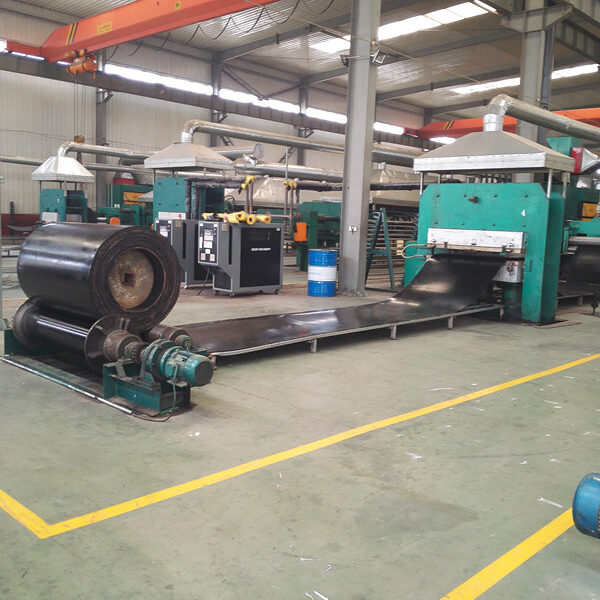
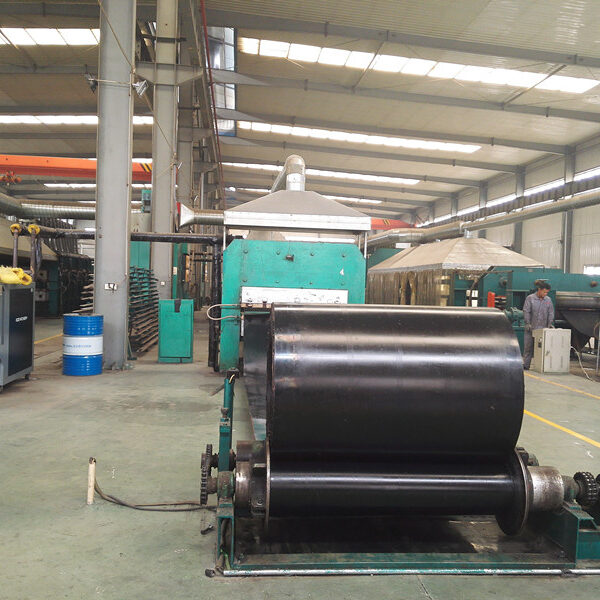
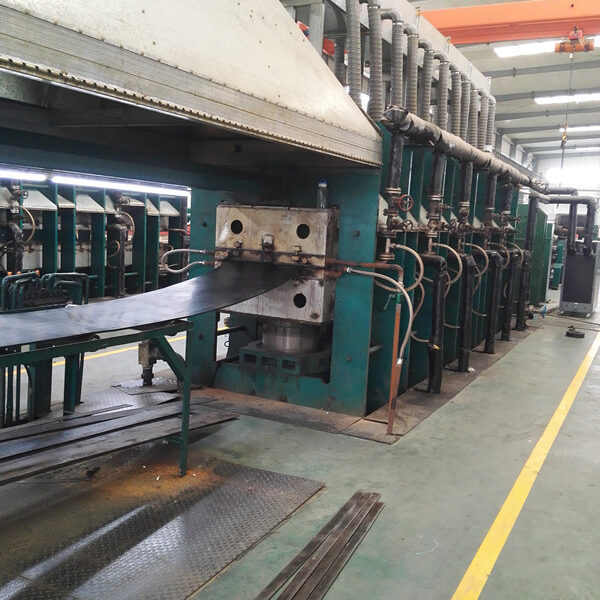
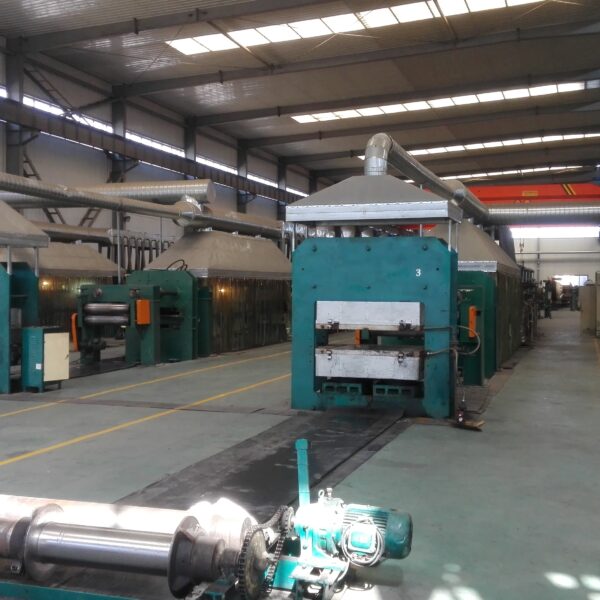

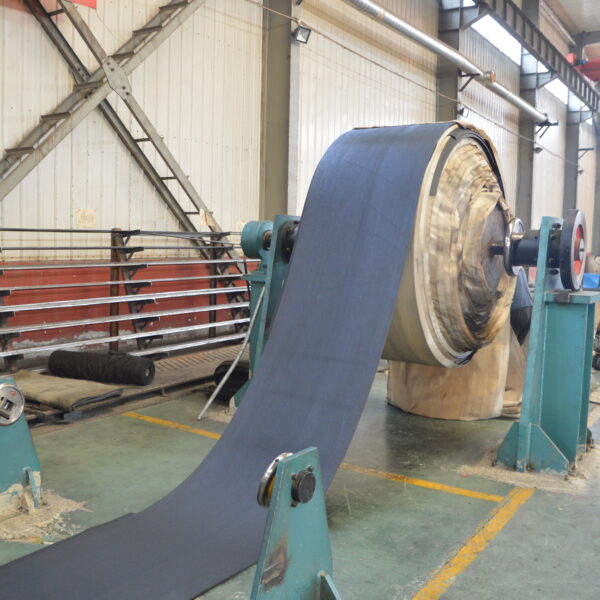
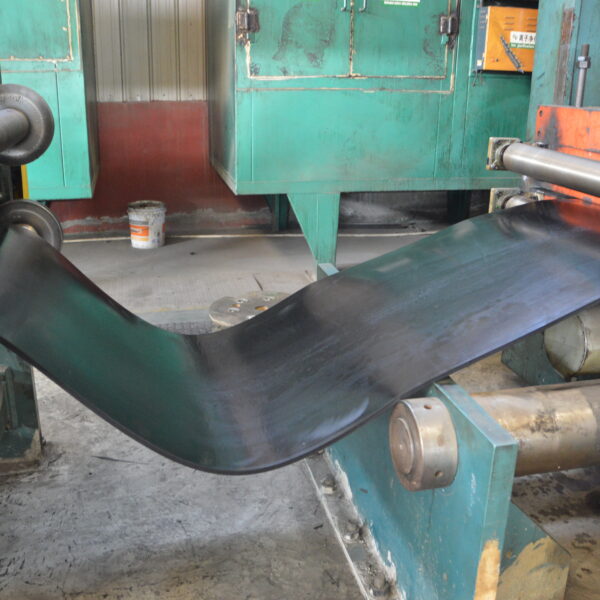
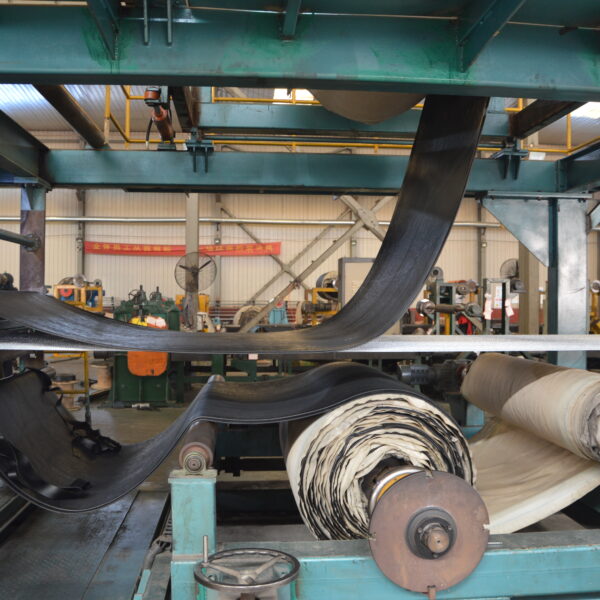
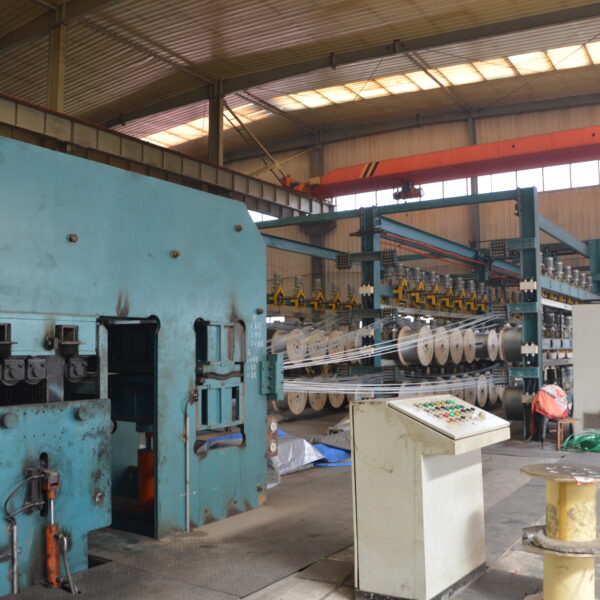
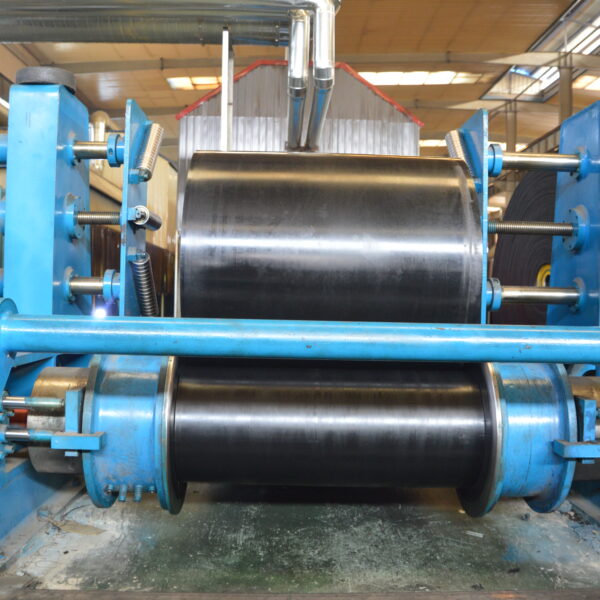
I. Rubber Conveyor Belt Production Process**
1. Raw Material Preparation
– **Compound Formulation**: Design rubber formulas based on application (heat-resistant, oil-resistant, anti-static), including:
– **Natural Rubber (NR)**: Provides elasticity.
– **Styrene-Butadiene Rubber (SBR)**: Enhances abrasion resistance.
– **Reinforcing Agents** (carbon black, silica): Improve tensile strength.
– **Anti-Aging Agents**: Extend service life.
– **Skeleton Material Treatment**:
– **Polyester Fabric (EP)** or **Steel Cords**: Treated with RFL (Resorcinol-Formaldehyde-Latex) dip to enhance rubber adhesion.
2. Mixing Process**
– **Equipment**: Internal mixer (e.g., GK-series Banbury mixer).
– **Procedure**:
1. Cut raw rubber into chunks and load into the mixer.
2. Add carbon black, plasticizers, vulcanizing agents, etc.
3. Mix at 120–160°C for 10–15 minutes to form homogeneous compound.
– **Key Controls**: Temperature, mixing time, filler dispersion.
3. Calendering & Forming
Equipment**: Four-roll calender (e.g., Φ700×1800mm).
– **Procedure**:
1. Feed the compound into the calender to form sheets of specified thickness.
2. **Lamination**: Bond rubber sheets with skeleton materials (polyester fabric/steel cords) to create the belt core.
3. **Top/Bottom Cover**: Apply wear-resistant and bonding layers to the core.
– **Parameters**: Roll temperature 80–100°C, line speed 10–30 m/min.
4. Vulcanization
Equipment**: Hydraulic plate vulcanizer (e.g., 5000-ton capacity).
– **Procedure**:
1. Place the belt preform into molds under 15–20 MPa pressure.
2. Vulcanize at 145–160°C for 30–60 minutes (time varies with thickness).
3. Achieve cross-linking for final properties.
– **Key Metrics**: Vulcanization curve (T90 time), pressure uniformity.
5. Cooling & Trimming
Equipment**: Water-cooling tank, automatic cutting machine.
– **Procedure**:
1. Cool vulcanized belts to <40°C in the water tank.
2. Trim edges and cut to length (±2mm tolerance).
3. Apply anti-stick agents (e.g., talcum powder).
6. Quality Testing
**Tests**:
– **Physical Properties**: Tensile strength (≥18 MPa), abrasion loss (≤90 mm³).
– **Safety**: Surface resistance (anti-static belts ≤3×10⁸ Ω).
– **Dimensions**: Width tolerance ±5 mm, thickness tolerance ±0.5 mm.
– **Equipment**: Tensile tester, abrasion tester, resistivity meter.
II. Key Process Optimization Points
1. **Temperature Control**:
– Mixing: Prevent scorching (<160°C).
– Vulcanization: Mold temperature variation <±2°C.
2. **Tension Control**:
– Calendering: Skeleton material tension fluctuation <3% to avoid wrinkles.
3. **Eco-Friendly Measures**:
– Mixing fumes treated via RTO (Regenerative Thermal Oxidizer), VOCs <30 mg/m³.
– Vulcanization emissions purified via alkaline scrubbers.